9 Effective Process Improvement Methodologies and How to Choose the Right One
In your organization, everyone is aligned, working toward the same goal: success. You’ve provided teams with the tools and resources they need to hit their targets. Employees are fully committed—often going the extra mile and putting in additional hours to ensure every KPI is met. Managers closely track performance, reporting on their teams’ progress. On the surface, everything seems to be running like a well-oiled machine.
Or so it appears.
Make no mistake—your success is real. But what if you could achieve the same results at a fraction of the cost? Studies show that companies lose between 20% and 30% of their revenue each year due to inefficiencies. Many businesses reach their goals without realizing they’re relying on outdated processes and ineffective workflows. The question isn’t whether you’re succeeding—it’s whether you’re doing it efficiently.
If that weren’t concerning enough, consider this: businesses lose up to 30% of their workforce’s time to unproductive tasks—like unnecessary meetings—caused by inefficient processes. Imagine employees still handling data entry as if it were 2002, wasting hours on manual tasks that could be automated. This doesn’t just inflate labor costs; it also drags down overall productivity.
Leveraging modern, scalable tools and systems is essential—it’s a core part of business process management, and we’ll dive deeper into that later. But for now, let’s focus on the quick wins: immediate, high-impact improvements you can implement with the right strategies.
This guide is designed to give you a clear, comprehensive understanding of the key process improvement methodologies businesses can implement to work smarter and more efficiently.
Table des matières
- What Is Process Improvement?
- Why Process Improvement Matters for Organizational Success
- Understanding Process Improvement Methodologies
- Popular Process Improvement Methodologies
- 1- Six Sigma: Data-Driven Quality Improvement
- 2- Lean: Maximizing Efficiency by Eliminating Waste
- 3- Total Quality Management (TQM): A Company-Wide Commitment to Excellence
- 4- Kaizen: Continuous Improvement Through Small, Incremental Changes
- 5- Business Process Reengineering (BPR): Radical Redesign for Maximum Efficiency
- 6- PDCA Cycle (Plan, Do, Check, Act)
- 7- Lean Six Sigma
- 8- Theory of Constraints (TOC)
- 9- Agile Methodology
- Process Improvement vs. Process Management: What’s the Difference?
- Steps for Implementing a Process Improvement Methodology
- Tools and Resources for Process Improvement
- Conclusion
- FAQs
What Is Process Improvement?
Process improvement is a structured approach to identifying, analyzing, and enhancing business processes to maximize efficiency and effectiveness. The goal is to optimize performance, eliminate waste, and boost overall productivity—all while maintaining or exceeding customer expectations for quality. This can involve streamlining workflows, integrating new technologies, or adopting industry best practices to make better use of resources.
Why Process Improvement Matters for Organizational Success
In today’s fast-paced, competitive landscape, businesses must continuously evolve to stay ahead. Process improvement plays a critical role in this by driving efficiency, reducing costs, and fostering a culture of innovation. Here’s how it benefits organizations:
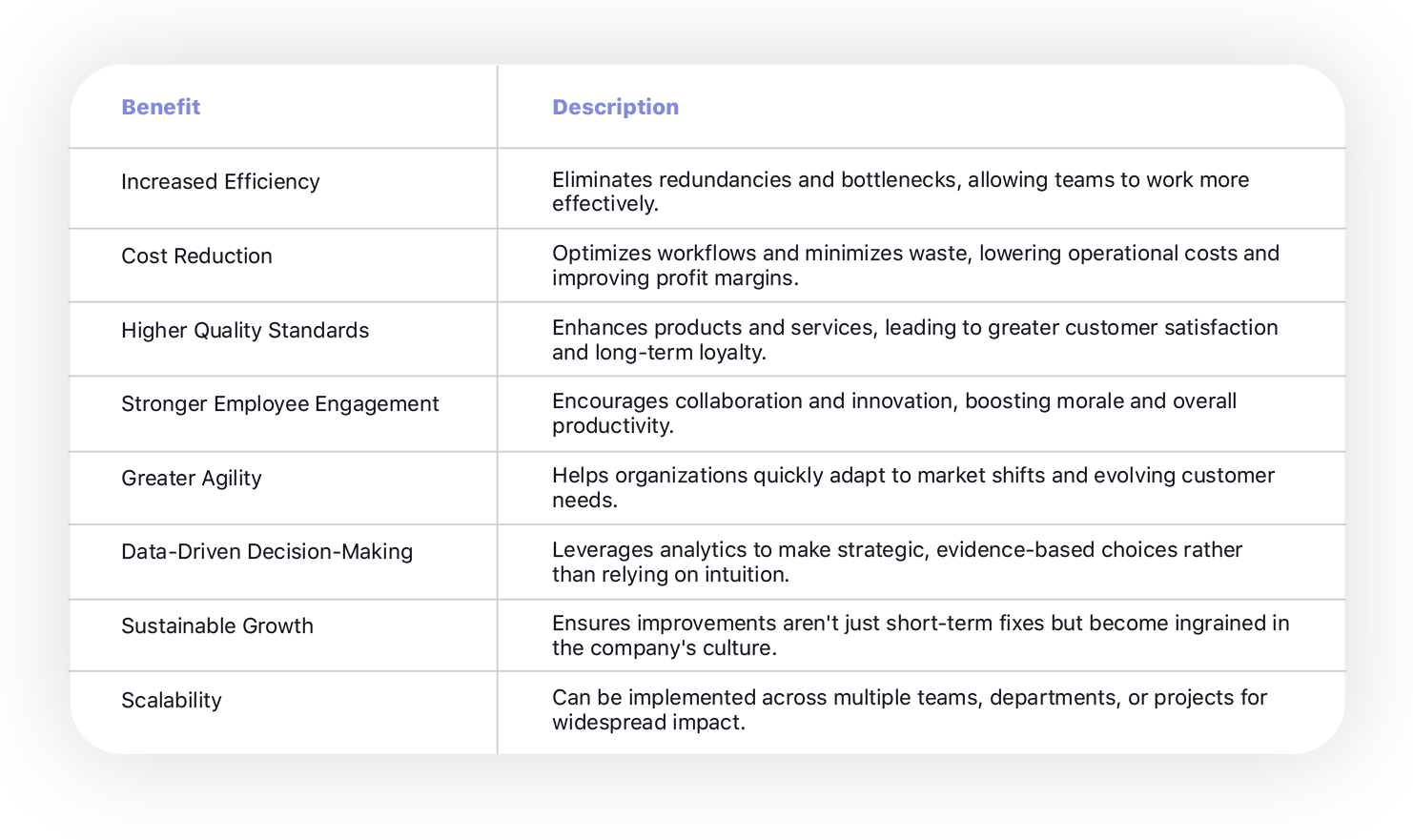
Understanding Process Improvement Methodologies
Process improvement methodologies are structured frameworks that help organizations systematically enhance their operations. Each methodology provides a set of principles, tools, and techniques designed to tackle specific challenges. By following these frameworks, teams can assess their current processes, identify inefficiencies, and implement improvements in a clear, measurable, and effective way.
Here’s how Lean transformed Toyota’s operations:
- Just-in-Time (JIT) Manufacturing – Instead of stockpiling excess inventory, Toyota produced only what was needed, exactly when it was needed, reducing waste and storage costs.
- Kaizen (Continuous Improvement) – Employees at all levels were encouraged to identify inefficiencies and suggest improvements, fostering a culture of innovation.
- Standardized Workflows – Processes were documented and optimized to ensure consistency, efficiency, and high-quality output.
- Visual Management (Kanban System) – Toyota introduced a visual workflow system to track progress, prevent bottlenecks, and enhance team coordination.
The results? Higher efficiency, lower costs, improved product quality, and a global reputation for operational excellence. Many industries today—beyond automotive manufacturing—have adopted Lean principles to improve their own processes, from healthcare to software development.
By learning from Toyota’s approach, businesses can apply Lean principles to their own workflows, ensuring they operate more efficiently while maintaining high-quality standards.
Popular Process Improvement Methodologies
Over time, various methodologies have been developed to tackle efficiency challenges, each offering a unique framework for process optimization. Some focus on data-driven strategies to reduce defects, while others emphasize continuous improvement and customer satisfaction.
The right approach depends on an organization’s specific goals, but ultimately, all aim to enhance the value chain and foster a culture of ongoing improvement.
1- Six Sigma: Data-Driven Quality Improvement
Originally developed by Motorola in 1986, Six Sigma is a methodology focused on improving processes by minimizing defects and reducing variability. The name “Six Sigma” comes from a statistical concept—where a process operates with fewer than 3.4 defects per million opportunities, achieving near-perfect efficiency. Over the years, Six Sigma has expanded beyond manufacturing, becoming a hallmark of quality management across industries, from healthcare to finance.
Core Principles: The DMAIC Framework
At the heart of Six Sigma is DMAIC, a structured, data-driven approach to process improvement:
- Define – Identify the problem and establish project goals.
- Measure – Collect data to assess current performance.
- Analyze – Investigate the data to uncover root causes of defects.
- Improve – Implement solutions to eliminate inefficiencies.
- Control – Establish measures to sustain long-term improvements.
By following this framework, organizations can systematically eliminate inefficiencies, enhance quality, and create a culture of continuous improvement.
Real-World Applications of Six Sigma
Six Sigma has been widely adopted across industries beyond manufacturing:
✅ Healthcare – Hospitals use Six Sigma to reduce patient wait times, streamline admissions, and enhance care quality.
✅ Finance – Banks apply Six Sigma to minimize transaction errors, improve service delivery, and boost customer satisfaction.
✅ Retail & Services – Companies use it to optimize supply chains, reduce waste, and enhance customer experiences.
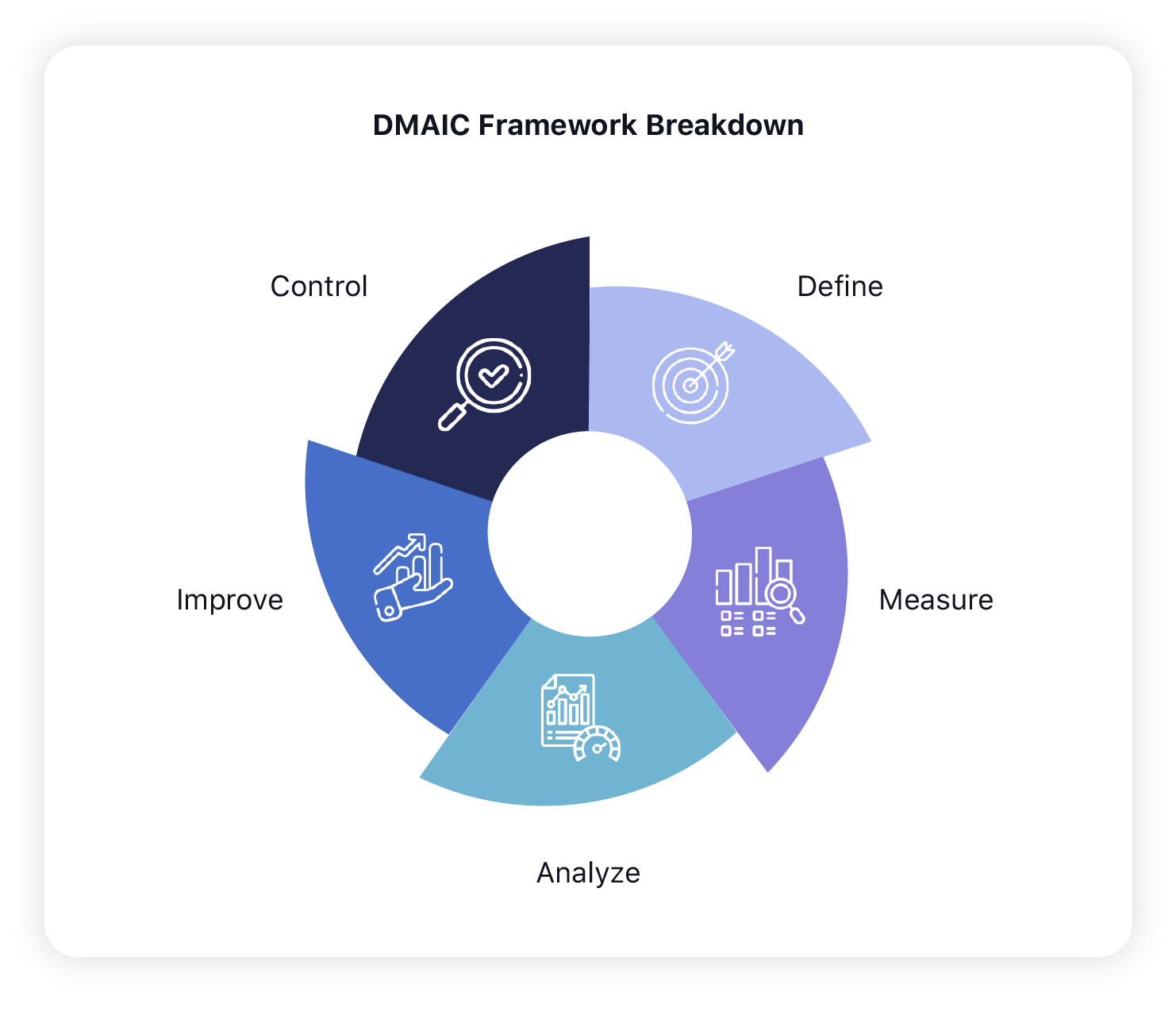
Best For:
Six Sigma is ideal for organizations that rely on rigorous data analysis and statistical methods to drive quality improvements. It’s particularly effective in manufacturing, healthcare, finance, and any industry where precision and defect reduction are critical to success.
2- Lean: Maximizing Efficiency by Eliminating Waste
Lean methodology originated from the Toyota Production System (TPS), a groundbreaking approach developed after World War II to optimize manufacturing by eliminating waste and enhancing efficiency. Originally designed to improve Toyota’s production processes, Lean has since been widely adopted across industries seeking operational excellence and resource optimization.
Core Principles: Waste Reduction & the 5S Methodology
At its core, Lean focuses on identifying and eliminating waste—known as “muda”—to maximize customer value. Waste can take many forms, including excess inventory, overproduction, long wait times, and product defects.
One of Lean’s essential tools is the 5S methodology, a structured approach to organizing workspaces and improving efficiency:
- Sort – Remove unnecessary items to declutter the workspace.
- Set in Order – Arrange essential tools and materials for easy access.
- Shine – Keep work areas clean and well-maintained.
- Standardize – Establish consistent processes for organization and maintenance.
- Sustain – Maintain these practices as part of the company culture.
By applying these principles, businesses streamline operations, improve workflow efficiency, and foster a culture of continuous improvement.
Real-World Applications of Lean
Lean principles have been successfully implemented across various industries:
✅ Aerospace – Boeing applied Lean practices to streamline assembly lines, reducing production time and improving delivery schedules.
✅ Healthcare – Hospitals use Lean to optimize patient flow, minimize wait times, and improve the quality of care.
✅ Retail & Logistics – Companies implement Lean strategies to enhance supply chain efficiency and reduce unnecessary inventory.
Best For:
Lean is ideal for organizations looking to boost efficiency by cutting waste and optimizing workflows. While it’s particularly effective in manufacturing, it has also been successfully applied in healthcare, logistics, service industries, and any sector where reducing inefficiencies leads to better resource utilization and faster delivery times.
3- Total Quality Management (TQM): A Company-Wide Commitment to Excellence
Total Quality Management (TQM) is a holistic approach to continuous improvement, focusing on enhancing product quality and customer satisfaction at every level of an organization. Unlike methodologies that target specific processes, TQM integrates quality improvement into the company’s culture, making it everyone’s responsibility—from executives to frontline employees.
Core Principle: Total Employee Involvement
A defining feature of TQM is total employee involvement, which encourages all team members to actively participate in decision-making and quality improvement efforts. By fostering a collaborative environment where every idea is valued, organizations can tap into collective insights, drive innovation, and achieve sustainable improvements.
Real-World Applications of TQM
TQM has been successfully implemented across various industries:
✅ Automotive – Ford Motor Company leveraged TQM to enhance quality control in its manufacturing plants, leading to fewer defects and higher customer satisfaction.
✅ Hospitality – The Ritz-Carlton Hotel Company applies TQM principles to ensure world-class service by prioritizing continuous training and employee engagement.
✅ Healthcare – Hospitals utilize TQM to improve patient care standards, reduce errors, and enhance overall efficiency.
Best For:
TQM is ideal for organizations committed to embedding quality at every level. It’s particularly effective in industries where customer satisfaction and service excellence are critical, such as hospitality, manufacturing, and healthcare, where employee engagement directly impacts quality outcomes.
4- Kaizen: Continuous Improvement Through Small, Incremental Changes
Kaizen, a Japanese term meaning “change for the better,” is a philosophy centered on continuous, small-scale improvements rather than large, disruptive overhauls. It promotes a mindset where employees at all levels are encouraged to identify inefficiencies and implement gradual, ongoing enhancements to optimize processes.
Core Principle: Small, Consistent Improvements for Lasting Impact
The essence of Kaizen lies in making minor adjustments regularly, which, over time, lead to significant efficiency and quality improvements. Instead of waiting for major process changes, organizations practicing Kaizen focus on continuous evaluation and refinement, fostering a culture of collaboration, innovation, and proactive problem-solving.
Real-World Applications of Kaizen
Kaizen has been successfully applied across multiple industries:
✅ Manufacturing – Toyota integrates Kaizen through Kaizen events—structured workshops that identify inefficiencies and drive productivity improvements on the assembly line.
✅ Hospitality – Restaurants apply Kaizen principles to streamline service workflows, reducing wait times and enhancing the customer experience.
✅ Healthcare – Hospitals use Kaizen to improve patient care, minimize waste in administrative processes, and boost operational efficiency.
Best For:
Kaizen is ideal for organizations seeking a low-risk, employee-driven approach to continuous improvement. It works particularly well in manufacturing, healthcare, service industries, and any environment that values ongoing process optimization without requiring major investments or disruptions.
5- Business Process Reengineering (BPR): Radical Redesign for Maximum Efficiency
Business Process Reengineering (BPR) is a management strategy focused on completely redesigning core business processes to achieve dramatic improvements in cost, quality, service, and speed. Unlike incremental improvement methods, BPR starts from scratch, challenging organizations to rethink how work is done and restructure workflows to eliminate inefficiencies. By aligning processes more closely with strategic objectives, businesses can significantly cut costs while improving overall performance.
Core Principle: Radical Transformation Over Incremental Change
While many process improvement methodologies focus on small, continuous refinements, BPR takes a bold approach—advocating for complete process overhauls. This method allows organizations to break away from outdated practices and design workflows that are more streamlined, effective, and aligned with modern business demands.
Challenges in BPR Implementation
Despite its potential for transformation, implementing BPR comes with challenges:
🚧 Employee Resistance – Radical process changes can face pushback from employees accustomed to existing workflows.
🚧 Operational Disruptions – Redesigning processes can temporarily impact productivity during the transition.
🚧 Technology Alignment – Integrating new workflows with existing systems can be complex.
🚧 Stakeholder Buy-In – Securing leadership and employee support is essential for successful implementation.
Strong leadership, clear communication, and change management strategies are crucial for overcoming these hurdles and ensuring a smooth transition.
Real-World Applications of BPR
One of the most well-known examples of BPR in action is Ford Motor Company’s overhaul of its accounts payable system in the 1990s. By eliminating traditional invoices and allowing suppliers to input data directly into Ford’s system, the company:
✅ Reduced workforce requirements by 75% in the accounts payable department
✅ Cut operational costs
✅ Streamlined supplier transactions for greater efficiency
BPR is best suited for organizations facing significant inefficiencies that require a complete overhaul of their business processes. It’s particularly effective when incremental improvements aren’t enough to resolve deep-rooted inefficiencies, making it ideal for industries needing large-scale transformation in efficiency, cost reduction, and service quality.
6- PDCA Cycle (Plan, Do, Check, Act)
The PDCA cycle is a structured, iterative framework for continuous improvement, consisting of four key steps: Plan, Do, Check, and Act. Originally developed by Walter Shewhart and later popularized by W. Edwards Deming, PDCA provides a systematic approach for identifying areas of improvement, implementing changes, and refining processes over time. Its cyclical nature ensures ongoing optimization, helping organizations stay agile and responsive.
How the PDCA Cycle Works
PDCA follows a data-driven approach to problem-solving and improvement:
🔹 Plan – Identify an issue or opportunity for improvement, then develop a strategy based on insights and hypotheses.
🔹 Do – Implement the planned changes on a small scale to test their effectiveness.
🔹 Check – Evaluate the results against objectives to determine whether the changes had the desired impact.
🔹 Act – Standardize successful changes or refine the approach before applying improvements on a larger scale.
Since PDCA is a continuous loop, organizations can repeatedly refine their processes, ensuring ongoing progress rather than one-time fixes.
Best For:
The PDCA cycle is ideal for organizations seeking a simple yet powerful framework for continuous improvement. It works particularly well when testing small-scale changes before broader implementation, making it valuable in manufacturing, service industries, healthcare, and business operations that prioritize efficiency and adaptability.
7- Lean Six Sigma
Lean Six Sigma blends the efficiency-driven approach of Lean with Six Sigma’s data-focused quality control, creating a powerful methodology for optimizing processes. By combining these two frameworks, organizations can eliminate waste, reduce defects, and enhance overall performance—leading to faster results and consistently high-quality outcomes.
How Lean Six Sigma Works
The synergy between Lean and Six Sigma offers a balanced approach to process improvement:
✔ Lean focuses on eliminating waste, ensuring that every step in a process adds value.
✔ Six Sigma emphasizes reducing variability and defects through statistical analysis.
By applying both methodologies together, organizations streamline operations, cut unnecessary costs, and improve product or service quality—all of which drive greater customer satisfaction and long-term efficiency.
Real-World Application
A prime example of Lean Six Sigma’s success is General Electric (GE), which leveraged the methodology to enhance manufacturing efficiency, reduce cycle times, and improve quality. This initiative resulted in billions of dollars in savings and positioned GE as a leader in operational excellence.
Best For:
Lean Six Sigma is ideal for organizations seeking a data-driven, end-to-end approach to process improvement. It works particularly well in industries where both efficiency and precision are critical, such as manufacturing, healthcare, finance, and logistics.
8- Theory of Constraints (TOC)
The Theory of Constraints (TOC) is a process optimization philosophy centered around identifying and eliminating bottlenecks that restrict an organization’s performance. Developed by Dr. Eliyahu M. Goldratt in his book The Goal, TOC asserts that every system has at least one critical constraint—and improving that weak link leads to significant gains in efficiency and productivity.
How TOC Works
TOC focuses on pinpointing constraints—whether they stem from limited resources, outdated policies, or inefficient workflows—and systematically resolving them. By directing efforts toward the most critical bottlenecks, organizations can:
✔ Maximize throughput (the rate at which work is completed)
✔ Reduce operational costs by optimizing resource allocation
✔ Minimize excess inventory by improving process flow
Real-World Application
TOC has been widely applied in manufacturing, where identifying and resolving constraints has led to faster production cycles and reduced waste. For example, companies use TOC to restructure assembly lines, improve supply chain logistics, and enhance production planning, ultimately driving greater efficiency and profitability.
Best For:
TOC is ideal for organizations struggling with process bottlenecks that limit overall performance. While especially effective in manufacturing, it also applies to logistics, healthcare, and service-based industries where workflow efficiency is crucial.
9- Agile Methodology
Agile methodology is a flexible, iterative approach to project management that emphasizes adaptability, collaboration, and continuous customer feedback. Instead of following a rigid, linear plan, Agile breaks projects into smaller, manageable cycles called sprints—typically lasting two to four weeks—allowing teams to adjust quickly to changing requirements and deliver incremental progress.
Why Agile Works
Agile’s core strength lies in its adaptability. Rather than adhering to a fixed plan, teams continuously gather feedback, reassess priorities, and refine their approach throughout the project lifecycle. This ensures:
✔ Faster delivery of working solutions
✔ Improved responsiveness to stakeholder needs
✔ Greater collaboration between cross-functional teams
✔ Continuous improvement based on real-time insights
Real-World Application
Agile is widely used in software development, where rapid iteration and evolving requirements demand flexibility. However, its principles have also been successfully adopted in marketing, product development, and other fast-paced industries where adaptability is key to success.
Best For:
Agile is ideal for organizations that operate in dynamic environments where priorities shift frequently. It’s particularly effective in software development, marketing, and product management, where teams need the agility to respond to customer feedback and market changes in real time.
Process Improvement vs. Process Management: What’s the Difference?
These two terms are often confused, but they represent distinct concepts. Here’s a clear breakdown of their differences:
✔ Process Improvement focuses on enhancing existing workflows—identifying inefficiencies, reducing costs, and improving quality. It’s about making current processes more effective and efficient.
✔ Business Process Management (BPM), on the other hand, is a broader, ongoing approach to managing processes across an organization. It involves defining, modeling, executing, monitoring, and optimizing workflows to align with business goals. BPM incorporates various improvement methodologies while leveraging technology to streamline operations and drive continuous improvement.
Why Process Management Matters
BPM isn’t just about fixing inefficiencies—it’s about structuring processes for long-term success. Organizations that implement strong BPM strategies see major efficiency gains:
- Companies that effectively reduce process time cycles experience a 20-50% boost in efficiency and are 2.5 times more likely to lead their industry.
- Streamlined workflows can save an average of 270 hours per employee in the first year alone.
- These time savings translate into significant financial benefits—estimated “soft savings” of $7,924 per process improvement, based on the value of recovered employee time.
By combining process improvement with a structured BPM approach, businesses maximize efficiency, minimize errors, and enhance overall productivity—all while staying adaptable in an ever-changing market.
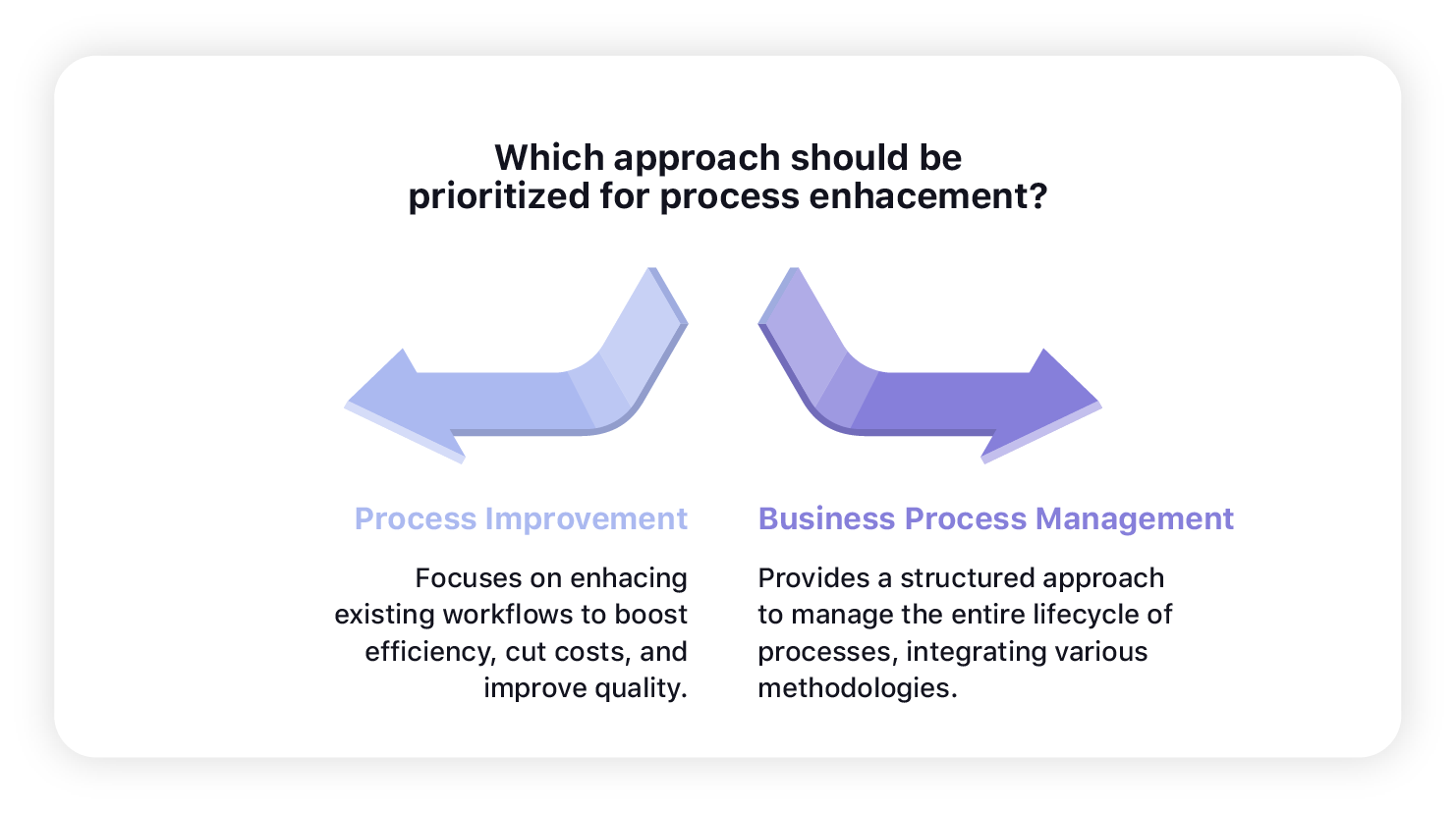
Steps for Implementing a Process Improvement Methodology
Successfully implementing a process improvement methodology requires a structured approach. Below are six key steps to guide your organization through the process:
1. Identifying Problem Areas Within Current Processes
- Conduct assessments through employee feedback, performance metrics, and process audits to pinpoint inefficiencies or bottlenecks.
- Engage team members directly involved in the process to gain valuable insights.
- Example: A retail company discovers through employee surveys that long checkout times are leading to customer dissatisfaction.
2. Mapping Existing Processes to Visualize Workflows
- Use flowcharts or diagrams to visually map out workflows and identify redundancies or unnecessary steps.
- This visualization helps stakeholders better understand how work progresses and where inefficiencies exist.
- Example: A manufacturing firm employs value stream mapping to identify delays in its production line.
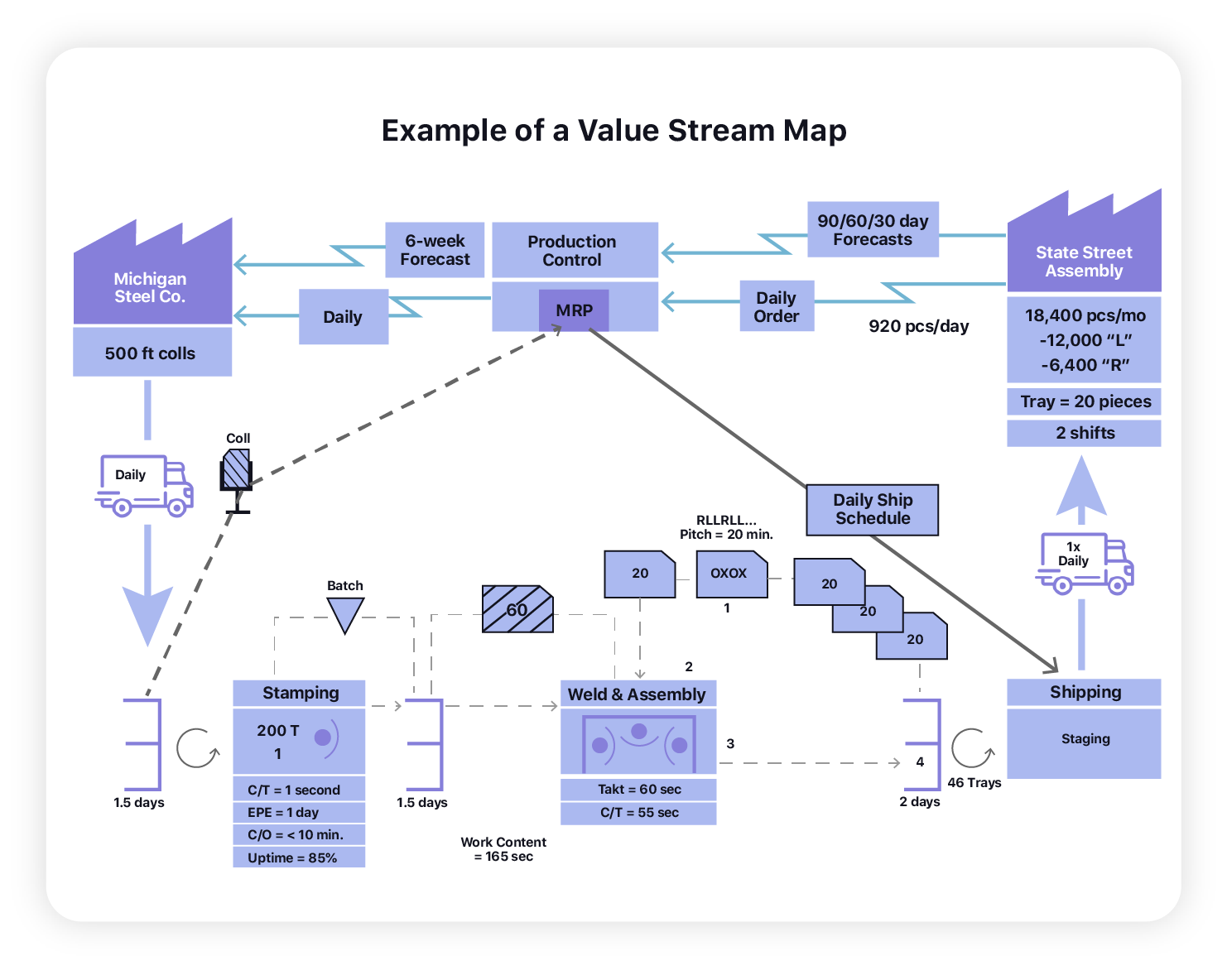
3. Setting Measurable Goals for Improvement
- Establish clear, quantifiable objectives that follow the SMART (Specific, Measurable, Achievable, Relevant, Time-bound) criteria.
- Well-defined goals provide a benchmark for evaluating success.
- Example: Reducing order processing time from 48 hours to 24 hours within three months.
4. Developing Solutions Collaboratively with Stakeholders
- Facilitate brainstorming sessions with key stakeholders to develop solutions for identified issues.
- Collaboration fosters buy-in and ensures a well-rounded approach to improvement.
- Example: A cross-functional team works together to enhance customer service by integrating new software tools for improved communication.
5. Monitoring Progress Through KPIs
- Implement key performance indicators (KPIs) to track the success of process improvements.
- Regularly review these metrics to ensure the desired results are being achieved.
- Example: A company measures customer satisfaction scores before and after refining its service delivery process.
6. Sustaining Improvements Over Time
- Integrate improvements into company culture through ongoing training, process reviews, and feedback loops.
- Establish dedicated teams to oversee long-term process enhancements.
- Example: A continuous improvement team meets quarterly to review and refine operational processes.
By following these structured steps, organizations can create a cycle of ongoing improvement, ensuring that operational efficiency continues to evolve in alignment with business goals.
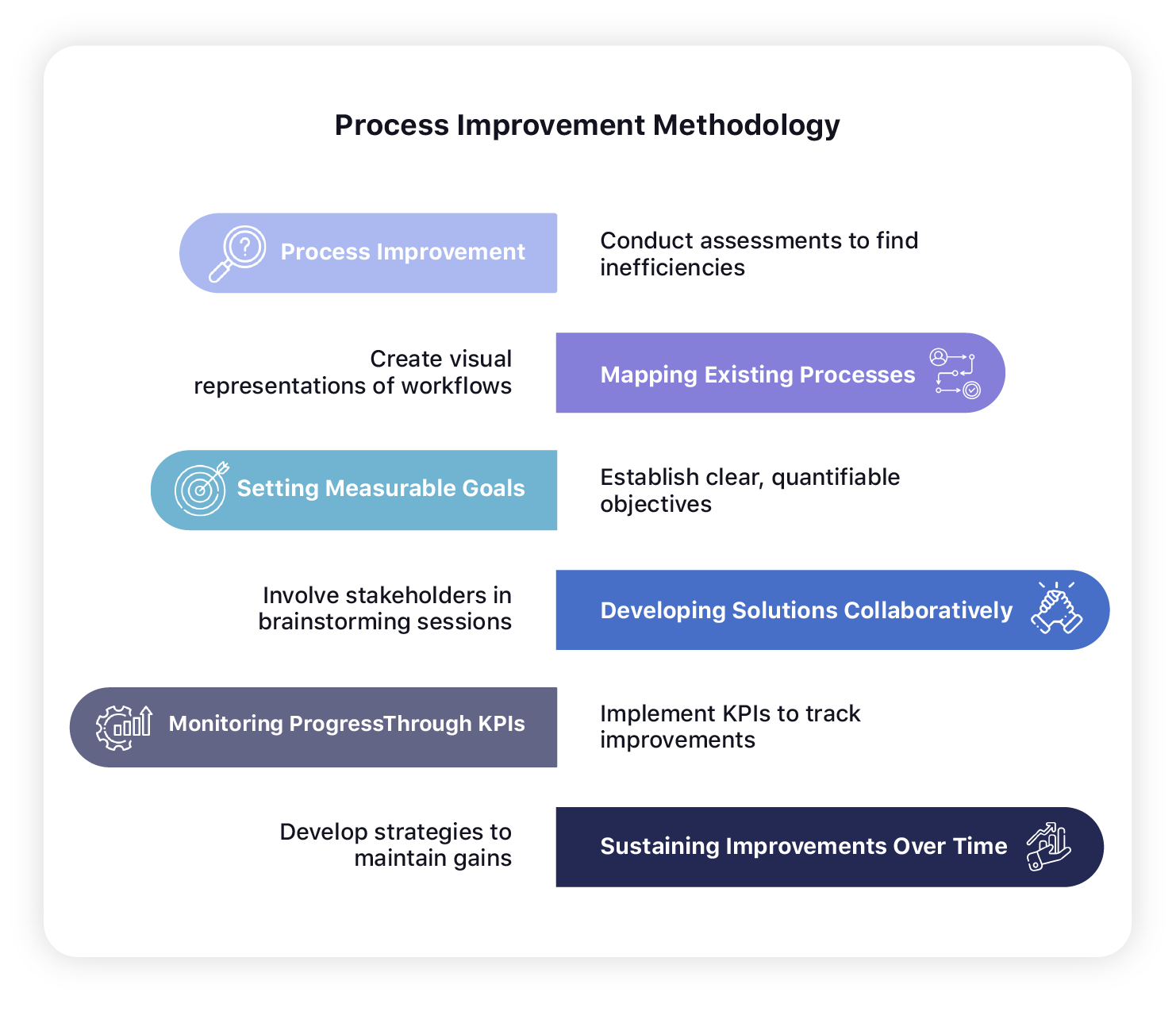
Tools and Resources for Process Improvement
Effective process improvement requires the right tools to track performance, manage workflows, and optimize resource allocation. One such tool is TrackingTime, a digital platform that helps organizations monitor time usage and boost productivity through real-time tracking and detailed reporting.
1- Time Tracking – Teams can log hours spent on specific tasks or projects, either as they work or retrospectively. This data helps pinpoint inefficiencies and identify areas for improvement.
2- Reporting – The platform generates comprehensive reports that visualize trends over time, allowing managers to make informed decisions about resource allocation and workload distribution.
3- Collaboration – TrackingTime enables team members to share updates and track project progress collectively, fostering better communication and coordination.
4- Integrations – The tool integrates with popular project management platforms like Asana and Trello, making it easy to incorporate into existing workflows without disruption.
At TrackingTime, we provide the expertise and tools you need to boost efficiency and future-proof your business processes.
Contact Us today to get started!
Conclusion
Process improvement methodologies are essential for organizations seeking to enhance efficiency, improve quality, and maintain a competitive edge. While the best methodology depends on your specific challenges and goals, the key is to take action and begin the journey toward continuous improvement.
FAQs
Identifying problem areas within your current workflows. This can be done through employee feedback, performance metrics, and process audits. Understanding inefficiencies or bottlenecks is crucial before implementing any changes.
Regularly, ideally on a quarterly or annual basis, to ensure ongoing efficiency. Frequent evaluations help processes remain effective, adapt to business needs, and align with organizational goals. Continuous monitoring sustains improvements over time.
Yes, process improvement methodologies can be combined for a more comprehensive approach. Lean Six Sigma is a prime example, merging Lean’s waste reduction principles with Six Sigma’s data-driven quality control to enhance efficiency and minimize defects. Organizations often tailor multiple methodologies to fit their specific needs.
If a process improvement methodology isn’t delivering expected results:
Reassess implementation: Ensure the methodology is being applied correctly and consistently.
Gather feedback: Engage employees and stakeholders to identify obstacles.
Make adjustments: Modify the approach based on real-time data and insights.
Explore alternatives: If necessary, switch to a methodology better suited to your challenges.
Lean and Lean Six Sigma are the primary methodologies focused on waste reduction.
Lean targets inefficiencies such as excess inventory, waiting times, and redundant steps.
Lean Six Sigma combines Lean’s waste elimination with Six Sigma’s quality improvement to enhance overall efficiency and performance.
1- Six Sigma: A data-driven approach focused on reducing defects and variability in processes.
2- Lean: A methodology that emphasizes eliminating waste and optimizing workflow efficiency.
Process improvement focuses on optimizing existing workflows to enhance efficiency, reduce costs, and improve quality. Business Process Management (BPM) is a broader approach that oversees the entire lifecycle of business processes, including modeling, execution, monitoring, and continuous improvement. While process improvement is a component of BPM, BPM ensures long-term process management and alignment with organizational objectives.
A Gemba Walk involves managers or leaders going to the actual workplace (Gemba) to observe processes, interact with employees, and identify areas for improvement. It provides real-world insights into operational inefficiencies and fosters collaboration between management and frontline workers.
Quality Circles are small groups of employees who regularly meet to identify, analyze, and solve work-related problems. These voluntary teams focus on continuous improvement, share best practices, and foster a culture of quality and teamwork.
Process Mapping visually represents workflows, helping organizations understand current processes, eliminate redundancies, and optimize operations. It serves as a foundation for process analysis and improvement initiatives.
Enterprise Resource Planning (ERP) Systems integrate business processes across departments, improving data visibility, reducing manual errors, and streamlining operations. They enhance efficiency by automating workflows and ensuring real-time access to information.
Automation reduces manual effort, minimizes errors, and speeds up repetitive tasks, allowing employees to focus on higher-value activities. It is widely used in areas like data entry, customer service, and manufacturing to improve accuracy and efficiency.